
大亞灣核電站及嶺澳核電站上充泵主推力瓦塊失效分析
來源:博高科技發(fā)布時間:2021/6/26
大亞灣核電站及嶺澳核電站上充泵
主推力瓦塊失效分析報告
編寫人: 朱青松
馬彥琦
張一偉
審核人:張可喜
審批人:朱禮進(jìn)
二0一二年十月二十二日
大亞灣核電站及嶺澳核電站上充泵主推力瓦塊失效分析
目錄
前言
1、 大亞灣及嶺澳核電站提供的已經(jīng)使用過的主推力瓦塊
2、 主推力瓦塊失效情況說明
3、 超聲波及著色探傷
4、 瓦塊厚度檢測
5、 瓦塊合金表面硬度的檢測
6、 合金成分分析
7、 損傷合金的掃描電鏡及低倍微觀觀察
8、 合金金相分析
9、 推力軸承承載能力分析
10、 推力軸承啟動及承載能力實(shí)驗(yàn)
11、 分析討論
前言
2011年10月20日,嶺澳核電站L1RCV003PO泵驅(qū)動端水平振動達(dá)6.8mm/s,超過報警值5.6mm/。2011年10月21日,解體泵驅(qū)動端軸瓦后發(fā)現(xiàn)一塊主推力瓦龜裂脫落。
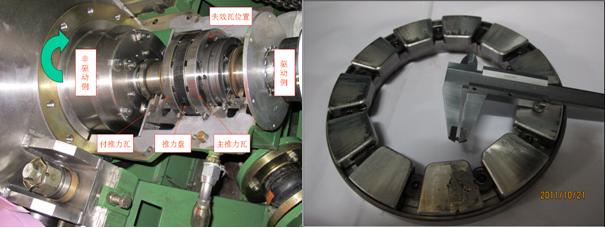
圖1 L1RCV003PO推力軸承檢修照片
2011年11月5日,大修期間對D2RCV001PO上充泵進(jìn)行了解體檢查,發(fā)現(xiàn)主推力軸承瓦面磨損嚴(yán)重,瓦面烏金向邊緣遷移碎裂。2011年10月以來,D2RCV001PO上充泵推力軸承溫度一直緩慢上漲。2011年10月7日,PT01RPA012試驗(yàn)中D1RCV001PO推力軸承最高溫度達(dá)到75℃,隨后推力軸承最高溫度基本穩(wěn)定在71.5度。2011年10月20日,D2RCV001PO推力軸承由64℃上漲到70℃以上。該推力軸承商運(yùn)后未更換過。大亞灣核電站商運(yùn)以來,D2RCV001PO上充泵在每兩月一次的定期試驗(yàn)中,輔助潤滑油泵和上充泵為同時啟動,而不是先啟動輔助潤滑油泵。
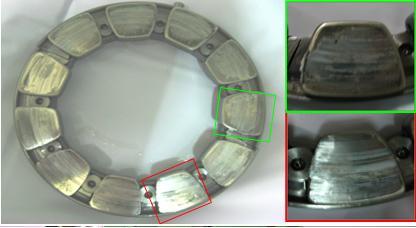
圖2 D2RCV001PO推力軸承檢修照片
2011年12月,根據(jù)反饋,對嶺澳核電站L2RCV001/002/003PO的推力軸承進(jìn)行解體檢查,其中更換了L2RCV002/003PO的所有主推力軸承。
2012年2月,上海大學(xué)軸承研究所赴大亞灣核電站L1RCV003PO上充泵檢修現(xiàn)場實(shí)地考察調(diào)研,檢查L1RCV003PO上充泵檢修推力軸承及軸承座檢修情況,測量實(shí)驗(yàn)室分析所需數(shù)據(jù),討論并確定軸瓦實(shí)驗(yàn)室分析樣品(D2RCV001PO主推力瓦9塊、L1RCV003PO主推力瓦11塊、L2RCV002PO主推力瓦11塊、L2RCV003PO主推力瓦11塊,新備件瓦1塊)。
一、大亞灣及嶺澳核電站提供的已經(jīng)使用過的主推力瓦塊
1、大亞灣D2RCV001PO位號的9塊主推力瓦塊,自編號為1號—9號。表面合金層有較明顯的遷移現(xiàn)象,在下圖的記號區(qū)域內(nèi)可以直接觀察到合金表面有細(xì)微的淺表性裂紋。(后來通過仔細(xì)觀察,照片中未做記號的一塊在相同位置也有細(xì)微的裂紋)
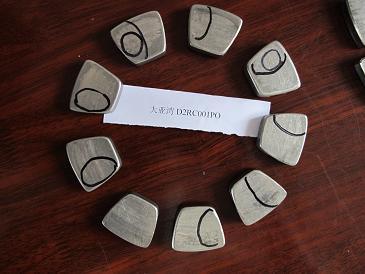
2、嶺澳1#機(jī)L1RCV003PO, 11塊主推力瓦塊,自編號為10號—20號。其中10號有嚴(yán)重龜裂;要求重點(diǎn)檢測10號及11號的巴氏合金和鋼背的結(jié)合情況。
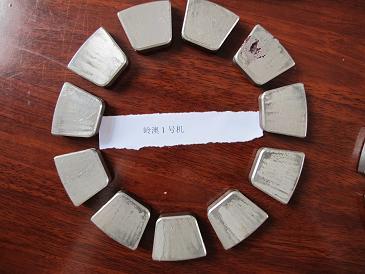
3、嶺澳2#機(jī) L2RCV002PO,11塊主推力瓦塊,自編號為21號—31號。
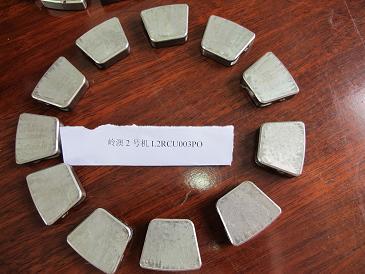
4、嶺澳2#機(jī) L2RCV003PO,11塊主推力瓦塊,自編號為32號—42號。
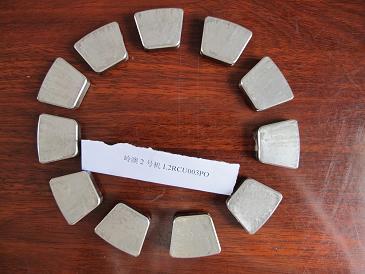
二、主推力瓦塊失效情況說明。
大亞灣核電站上充泵主推力軸承瓦塊發(fā)生合金層遷移現(xiàn)象以及細(xì)微的裂紋,嶺澳核電站上充泵主推力軸承瓦塊巴氏合金發(fā)生龜裂現(xiàn)象,如圖下圖所示。10號瓦塊合金面出現(xiàn)嚴(yán)重龜裂以及1-9號瓦塊合金表面出現(xiàn)細(xì)微的淺表性裂紋(,其共同特點(diǎn)都是在逆時針方向(推力盤相對于瓦塊旋轉(zhuǎn)方向)上的潤滑油出口側(cè)(如圖框選范圍內(nèi))發(fā)生龜裂。

10號瓦塊合金面在框選范圍內(nèi) 1-9號瓦塊表面合金層有較明顯的遷移現(xiàn)
出現(xiàn)嚴(yán)重龜裂 象以及合金表面在框選范圍內(nèi)有細(xì)微的
淺表性裂紋
三、 超聲波及著色探傷:對所有瓦塊進(jìn)行超聲波探傷以及著色探傷,判斷巴氏合金和鋼背的結(jié)合情況。
超
聲
探
傷 |
型號 |
探頭 |
頻率 |
量程 |
粗衰減 |
中衰減 |
微衰減 |
未發(fā)現(xiàn)
缺陷波 | |||
CTS-23B |
10C-6N
(6mm) |
5MHz |
10 |
0dB |
1.5dB |
20dB | |||||
著
色
探
傷 |
清洗劑 |
滲透劑 |
顯傷劑 |
滲透時間(分) |
結(jié)合面無裂縫 | ||||||
HD-BX |
HD-RS |
HD-XS |
30 | ||||||||
探傷結(jié)果為巴氏合金與鋼背結(jié)合邊緣沒有任何裂紋,結(jié)合面內(nèi)部沒有脫殼現(xiàn)象。
四、 對所有瓦塊的厚度進(jìn)行檢測。檢測量具為0-25mm壁厚千分尺。
每組瓦塊的厚度誤差會直接影響到各個瓦塊所承受的載荷。如果厚度誤差太大,設(shè)備運(yùn)行時會形成部分瓦塊承擔(dān)推力載荷,其余瓦塊不承擔(dān)推力載荷的現(xiàn)象,這樣會導(dǎo)致部分瓦塊載荷過大運(yùn)行溫度升高,甚至?xí)霈F(xiàn)燒瓦現(xiàn)象,因此應(yīng)該盡量減小同組瓦塊的厚度誤差。由于機(jī)械制造總會出現(xiàn)誤差,通常同組推力瓦塊的厚度誤差應(yīng)小于0.01mm。
1、大亞灣D2RCV001PO位號的9塊主推力瓦塊,自編號為1號—9號
編號 |
1 |
2 |
3 |
4 |
5 |
6 |
7 |
8 |
9 |
厚度(mm) |
11.03 |
11.025 |
11.02 |
11.038 |
11.036 |
11.043 |
11.03 |
11.012 |
11.04 |
該組最大厚度尺寸為11.043mm,最小厚度尺寸為11.012mm,有0.031mm誤差。由于各個瓦塊合金表面發(fā)生了遷移,會影響各個瓦塊的厚度尺寸,不能真實(shí)反映原始尺寸情況。
2、嶺澳1#機(jī)L1RCV003PO, 11塊主推力瓦塊,自編號為10號—20號
編號 |
10 |
11 |
12 |
13 |
14 |
15 |
16 |
17 |
18 |
19 |
20 |
厚度(mm) |
11.08 |
11.055 |
11.062 |
11.055 |
11.055 |
11.058 |
11.058 |
11.058 |
11.055 |
11.059 |
11.057 |
該組最大厚度尺寸為10號:11.08mm,由于10號合金表面有嚴(yán)重裂紋,所測尺寸不做比較。10號之外最大厚度尺寸為11.062mm,最小厚度尺寸為11.055mm,有0.007mm誤差。各個瓦塊的最大厚度誤差小于0.01mm,比較均勻。
3、嶺澳2#機(jī) L2RCV002PO,11塊主推力瓦塊,自編號為21號—31號
編號 |
21 |
22 |
23 |
24 |
25 |
26 |
27 |
28 |
29 |
30 |
31 |
厚度(mm) |
11.059 |
11.059 |
11.057 |
11.06 |
11.06 |
11.057 |
11.058 |
11.06 |
11.055 |
11.06 |
11.059 |
該組最大尺寸為11.06mm,最小尺寸為11.055mm,有0.005mm誤差。各個瓦塊的厚度誤差小于0.01mm,比較均勻。
4、嶺澳2#機(jī) L2RCV003PO,11塊主推力瓦塊,自編號為32號—42號。
編號 |
32 |
33 |
34 |
35 |
36 |
37 |
38 |
39 |
40 |
41 |
42 |
厚度(mm) |
11.058 |
11.059 |
11.059 |
11.06 |
11.06 |
11.058 |
11.058 |
11.06 |
11.058 |
11.06 |
11.056 |
該組最大尺寸為11.06mm,最小尺寸為11.056mm,有0.004mm誤差。各個瓦塊的厚度誤差小于0.01mm,比較均勻。
從以上尺寸檢查結(jié)果來看,每組瓦塊的厚度誤差小于0,01mm,是比較均勻的,個別瓦塊產(chǎn)生龜裂及細(xì)微裂紋可以排除因瓦塊制造所產(chǎn)生的厚度誤差而引起的。
五、 各個瓦塊巴氏合金表面硬度檢測。
巴氏合金具有摩擦相容性、嵌入性、磨合性; 摩擦順應(yīng)性、耐磨性、耐疲勞性、耐氣蝕性。巴氏合金的硬度直接影響巴氏合金以上的性能,也影響巴氏合金的抗壓強(qiáng)度。巴氏合金的成分以及巴氏合金的金相組織結(jié)構(gòu)直接影響巴氏合金的強(qiáng)度。
檢測儀器為里氏硬度計,型號為HL-600。
硬度單位:里氏HLD;
檢測標(biāo)準(zhǔn):GB/T17394-1998;
檢測部位為主推力瓦塊巴氏合金平面;每塊瓦塊檢測2點(diǎn)。
1、大亞灣D2RCV001PO的9塊主推力瓦塊,自編號為1號—9號
編號 |
1 |
2 |
3 |
4 |
5 |
6 |
7 |
8 |
9 |
測點(diǎn)1 |
235 |
197 |
242 |
212 |
205 |
268 |
211 |
254 |
234 |
測點(diǎn)2 |
222 |
229 |
227 |
181 |
212 |
228 |
202 |
238 |
278 |
平均值為:226.4HLD
2、嶺澳L1RCV003PO,11塊主推力瓦塊,自編號為10號—20號。
編號 |
10 |
11 |
12 |
13 |
14 |
15 |
16 |
17 |
18 |
19 |
20 |
測點(diǎn)1 |
253 |
277 |
220 |
241 |
252 |
237 |
216 |
240 |
224 |
203 |
266 |
測點(diǎn)2 |
213 |
240 |
207 |
233 |
261 |
209 |
259 |
203 |
236 |
278 |
299 |
平均值為:239.4HLD
3、嶺澳L2RCV002PO,11塊主推力瓦塊,自編號為21號—31號。
編號 |
21 |
22 |
23 |
24 |
25 |
26 |
27 |
28 |
29 |
30 |
31 |
測點(diǎn)1 |
271 |
256 |
275 |
276 |
254 |
261 |
266 |
232 |
292 |
294 |
241 |
測點(diǎn)2 |
262 |
296 |
211 |
247 |
280 |
258 |
275 |
294 |
244 |
216 |
266 |
平均值為: 262.1 HLD
4、嶺澳L2RCV003PO,11塊主推力瓦塊,自編號為32號—42號。
編號 |
32 |
33 |
34 |
35 |
36 |
37 |
38 |
39 |
40 |
41 |
42 |
測點(diǎn)1 |
287 |
233 |
249 |
243 |
260 |
231 |
268 |
252 |
268 |
231 |
259 |
測點(diǎn)2 |
282 |
242 |
224 |
244 |
214 |
243 |
239 |
264 |
230 |
244 |
212 |
平均值為: 246.3HLD
從以上檢測結(jié)果可知:大亞灣D2RCV001PO的9塊主推力瓦塊平均硬度為226.4HLD,為四組瓦塊中硬度最低的一組;嶺澳 L2RCV002PO,11塊主推力瓦塊的平均硬度為262.1 HLD,為四組瓦塊中硬度最高的一組。(表中有的瓦塊兩點(diǎn)硬度誤差較大的原因可能是金相組織不均勻形成的)
六、 推力瓦塊巴氏合金的成分分析
對推力瓦塊巴氏合金的成分分析是判斷其成分是否有異常情況、是否符合標(biāo)準(zhǔn)牌號的合金成分。成分分析采用化學(xué)分析和能譜分析兩種方法
取樣。每組推力瓦塊選取一塊進(jìn)行切割取樣,各組瓦塊分別選取7號、10號、21號、34號,如下圖示:圓形框選為切割區(qū)域,提供能譜分析之用,方形框選為取樣巴氏合金(后增加11號、12號、18號),為化學(xué)分析之用。
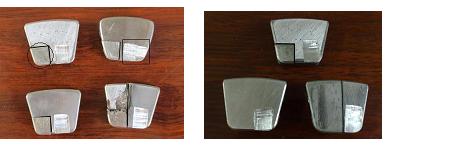
1、 化學(xué)成分分析
分析方法 :電感耦合等離子體原子發(fā)射光譜
分析儀器:PE 公司Optima 7300DV
各個取樣試件主要化學(xué)成分如下表所示:
|
Cu |
Sb |
Cd |
余量Sn |
7 號 |
3.58 |
6.97 |
0.00058 |
89.45 |
10號 |
1.81 |
8.07 |
0.23 |
89.89 |
11號 |
1.69 |
7.16 |
0.23 |
90.92 |
12號 |
1.56 |
7.26 |
0.25 |
90.93 |
18號 |
1.73 |
7.56 |
0.26 |
90.45 |
21號 |
3.80 |
7.56 |
0.43 |
88.21 |
34號 |
3.59 |
7.39 |
0.49 |
88.53 |
表中合金成分與標(biāo)準(zhǔn)牌號ZSnSb8Cu4(Sb:8%;Cu:4%;Cd:1%;Sn:87%)比較符合,但10號、11號、12號、18號瓦塊銅的含量偏低。
2、 能譜成分分析
分析方法:能譜、樣件全表面
分析儀器:S-570 Scanning Electron Microscope
將7號、10號、21號、34號每塊瓦塊切取15mmX15mm大小的試件,對其巴氏合金層的全表面進(jìn)行能譜分析,結(jié)果如下:
7號試件 10號試件
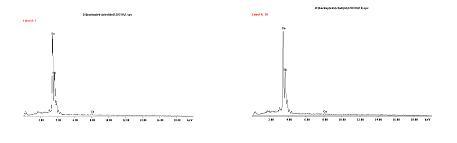
21號試件 34號試件
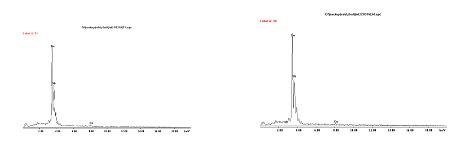
各個檢測件成分如下表:
合金成分
試件號 |
Sn |
Sb |
Cu |
與巴氏合金ZSn8Cu4相比較 |
7號瓦塊 |
87.81 |
8.7 |
3.5 |
Sb:8%
Cu:4% |
10號瓦塊 |
89.2 |
9.29 |
1.51 | |
21號瓦塊 |
87.43 |
9.05 |
3.52 | |
34號瓦塊 |
88.48 |
9.15 |
2.35 |
由能譜測量結(jié)果可知: 7號、10號、21號、34號的合金成分基本符合標(biāo)準(zhǔn)牌號中的ZSn8Cu4要求,但是Cu的含量偏低。由于能譜只能分析取樣試件巴氏合金表面幾微米深度的合金成分,各個瓦塊中Cu的含量相差較大與合金成分的偏析(組織不均勻)也有很大的關(guān)系,這在后面分析的金相組織顯微圖中可以明顯看出。10號瓦塊Cu含量只有1.51%,與化學(xué)分析結(jié)果相近。
合金中銅(Cu)的含量偏低會導(dǎo)致巴氏合金中硬質(zhì)相SnSb和Cu6Sn5的減少,對力學(xué)性能直接的影響便是硬度的下降。
軸瓦合金材料成分與 GB1174-1992 ZSnSb8Cu4 化學(xué)成分相近,ZSnSb8Cu4 常應(yīng)用于重
載機(jī)器的推力軸承。與國家標(biāo)準(zhǔn)及其它電站瓦塊材料成分比較,軸瓦硬度未見異常,但合金Cu 含量偏低,會降低合金的耐疲極限。
七、 推力瓦塊巴氏合金的掃描電鏡微觀形貌及低倍微觀形貌觀察
掃描電鏡微觀形貌:
分析儀器:S-570 Scanning Electron Microscope
低倍微觀形貌觀察:
分析儀器:BJ-A
5號瓦塊在框選范圍內(nèi)合金表面顯微圖像(400倍放大)
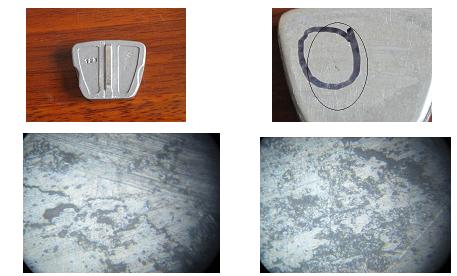
合金表面有細(xì)微的裂紋 合金表面有微熔
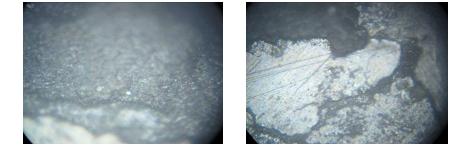
合金表面有微熔 合金表面有明顯的裂紋
6號瓦塊在框選范圍內(nèi)合金表面顯微圖像(400倍放大),在切割范圍內(nèi)電鏡觀察表面遷移圖像

合金表面有微熔
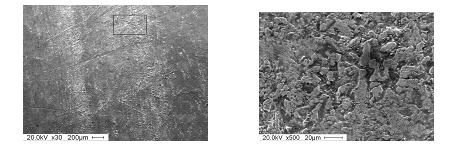
圖中白色部分是合金表面磨痕30倍電鏡放大 為左圖方形框選區(qū)域500倍電鏡放大
5號瓦塊、6號瓦塊是大亞灣上充泵D2RCV001PO位號的主推力瓦塊,從顯微照片中可以明顯看出合金層表面開始產(chǎn)生熔融和細(xì)微的龜裂。
10號瓦塊的表面顯微圖像(200放大)及電鏡掃描圖像,10號瓦塊是嶺澳L1RCV003PO中的一塊瓦塊,是損傷最嚴(yán)重的瓦塊
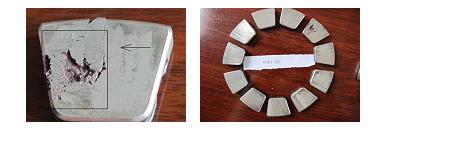
10號瓦塊及其同組瓦塊
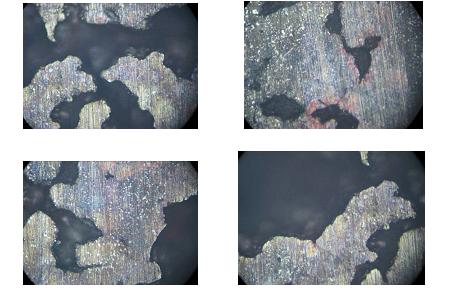
以上為10號瓦塊表面微觀顯微圖像(200倍)
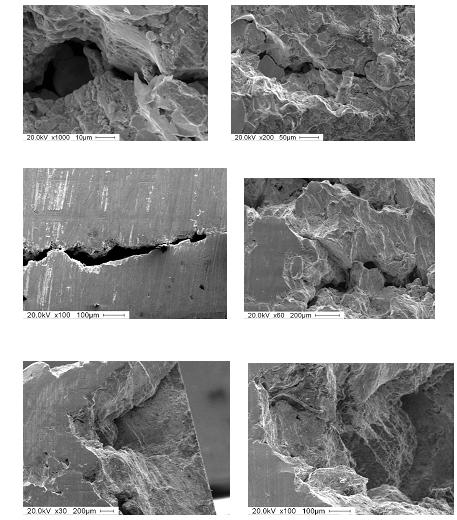
以上為10號瓦塊電鏡掃描圖像
10號瓦塊從宏觀照片可直接看出瓦塊合金面出現(xiàn)龜裂現(xiàn)象,這因高溫和壓力聯(lián)合作用下引起的疲勞龜裂現(xiàn)象。
從10號瓦塊表面微觀顯微圖像(200倍)中,合金表面因高溫引起合金金相不規(guī)則的熱熔現(xiàn)象。
對10號瓦塊斷面做電鏡掃描,可觀察到斷口表面嚴(yán)重氧化、斷口陳舊且受污染,觀察不到韌窩以及疲勞斷裂的輝紋。但可以觀察到裂紋是垂直于滑動方向向縱深發(fā)展的
八、 推力瓦塊合金金相分析
金相儀器型號:BJ-A
腐蝕方法: 4%硝酸酒精擦拭
拋光方法: 機(jī)械拋光
執(zhí)行標(biāo)準(zhǔn): GB/T 13298-91
金相組織: α+SnSb+Cu6Sn5
此項(xiàng)分析是直接從微觀上觀看巴氏合金斷面及金相組織分布情況,判斷巴氏合金鑄造的優(yōu)良性。
1、 上充泵7號瓦塊金相照片(200倍)
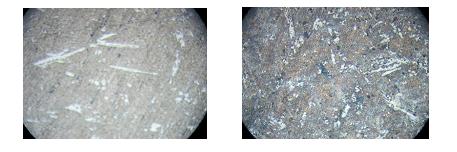
圖中方形化合物SnSb(白色),以及白色針狀和星狀化合物Cu6Sn5很少,組織分布明顯異常
2、上充泵10號瓦塊金相照片(200倍)
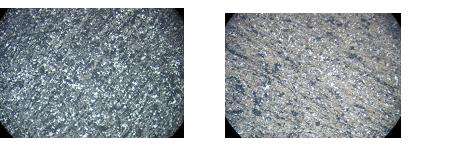
方形化合物SnSb(白色)很小,沒有白色針狀和星狀化合物Cu6Sn5,左右圖對比組織不均勻
3、 上充泵11號瓦塊金相照片(200倍)
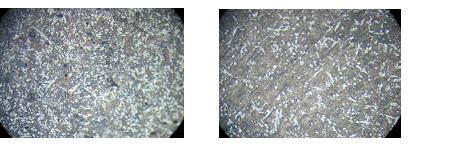
方形化合物SnSb(白色)很少,左右圖對比組織不均勻
4、 上充泵17號瓦塊金相照片(200倍)

方形化合物SnSb(白色)很少,沒有白色針狀和星狀化合物Cu6Sn5,左右圖對比組織不均勻
5、 上充泵18號瓦塊金相照片(200倍)
方形化合物SnSb(白色)很少
6、 上充泵34號瓦塊金相照片(200倍)
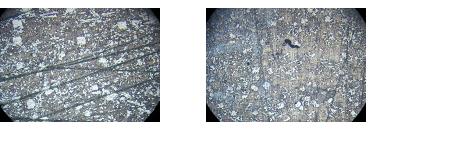
圖中方形化合物SnSb(白色),以及白色針狀和星狀化合物Cu6Sn5正常,組織分布未見明顯異常
從各個瓦塊金相組織上看,上充泵各個瓦塊組織差異很大,組織不均勻。
7、從10號瓦塊及11號瓦塊的截斷的金相觀察合金與鋼背的結(jié)合情況
直接將10瓦塊和11號瓦塊一分為二,再觀察10號瓦塊和11號瓦塊的斷截面的顯微情況。
10號瓦塊的斷截面顯微圖像(200倍放大)
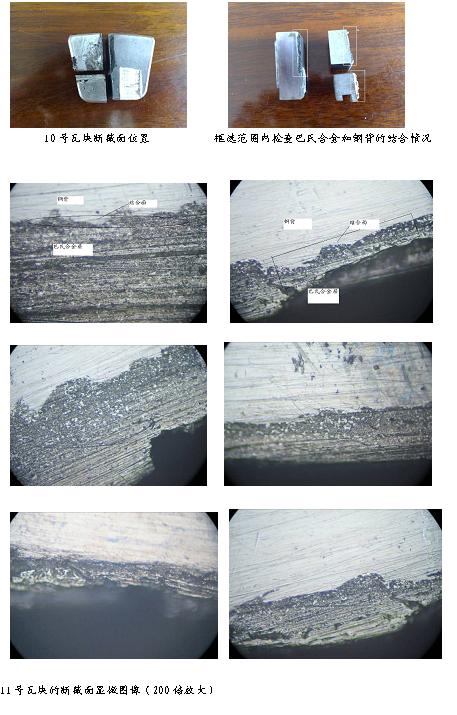
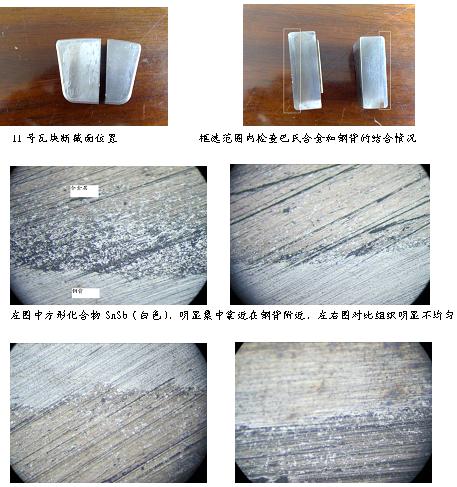
左圖中方形化合物SnSb(白色)很少
從10號、11號瓦塊斷截面顯微圖片可以看出巴氏合金層和鋼背的結(jié)合是良好的沒有裂縫,特別是10號瓦塊雖然巴氏合金層已經(jīng)很薄,但與鋼背的結(jié)合面上沒有分層現(xiàn)象,結(jié)合良好。11號瓦塊合金層和鋼背結(jié)合面沒有任何微觀分層現(xiàn)象,但從顯微照片可以看出金相組織嚴(yán)重偏析不均勻。
據(jù)此可以判斷10號瓦塊產(chǎn)生龜裂失效不是因合金層結(jié)合不良引起,而是由油膜高溫和及油膜壓力聯(lián)合作用下產(chǎn)生的龜裂現(xiàn)象。
巴氏合金的組織特點(diǎn)是,在軟相基體上均勻分布著硬相質(zhì)點(diǎn),軟相基體使合金具有非常好的嵌藏性、順應(yīng)性和抗咬合性,并在磨合后,軟基體內(nèi)凹,硬質(zhì)點(diǎn)外凸,使滑動面之間形成微小間隙,成為貯油空間和潤滑油通道,利于減摩;上凸的硬質(zhì)點(diǎn)起支承作用,有利于承載。上充泵每月一次在油泵沒有開啟、潤滑油沒有循環(huán)的情況下進(jìn)行緊急運(yùn)行測試,應(yīng)該是邊界潤滑狀態(tài),由于缺少潤滑油,轉(zhuǎn)子對上凸的硬質(zhì)點(diǎn)會產(chǎn)生研磨。
巴氏合金以錫銻組合的合金應(yīng)用最為廣泛,含銻(Sb)小于9%的合金凝固后的組織為Sb溶于錫(Sn)中的單一相——α固溶體;當(dāng)Sb含量超過9%時,合金中將結(jié)晶析出化合物SnSb(呈立方體形,在金相顯微鏡下通常呈方形)。這類合金在常溫下的金相組織為軟基體α固溶體+硬質(zhì)相SnSb,由于初晶體SnSb比較輕,因而易于上浮產(chǎn)生比重偏析。合金中化學(xué)成分和組織組成物不均勻的現(xiàn)象叫做偏析。由于偏析,勢必造成合金各部分物理、化學(xué),機(jī)械性能的不一致,降低軸瓦的內(nèi)在質(zhì)量和使用壽命。
經(jīng)檢驗(yàn),推力軸瓦主要金相組織為α+Cu6Sn5,與ZSnSb8Cu4 金相組織一致,且符合要求。與ZSnSb8Cu4 標(biāo)準(zhǔn)金相組織比較,組織分布不均勻,存在輕微偏析現(xiàn)象,但未見合金脫胎缺陷。
九、 推力軸承承載能力分析
通過計算分析可以判斷推力軸承承載能力的大小以及推力瓦塊的結(jié)構(gòu)是否合理
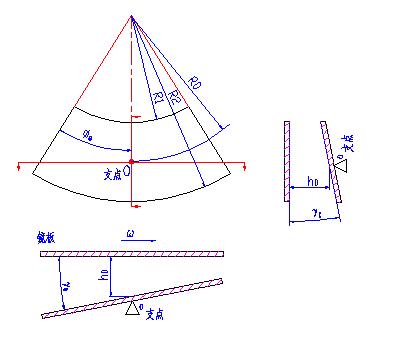
可傾瓦瓦塊幾何形狀和油楔幾何形狀
(一)、理論分析
1、 膜厚方程
O為瓦塊支點(diǎn),瓦塊繞O點(diǎn)作徑向及周向傾斜。
不考慮瓦塊的彈性變形,油膜厚度的函數(shù)表達(dá)式為:

其中:
-瓦塊支點(diǎn)處的油膜厚度
-瓦塊支點(diǎn)處的半徑


-瓦塊的徑向和周向的傾斜角 -支點(diǎn)與進(jìn)油邊的夾角
由流體力學(xué)原理,可以推導(dǎo)出二維雷諾(Reynolds)方程如下:
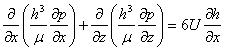
化為圓柱坐標(biāo)形式如下:

-推力軸承鏡板角速度
而對于二維雷諾方程難以直接通過解析法求解得出壓力分布的統(tǒng)一公式,所以其求解必須借助于數(shù)值計算方法(如有限差分法),即先確定承載區(qū)四周邊界的壓力分布,進(jìn)而利用邊值問題的求解方法獲得整個區(qū)域的壓力分布。
2、 能量方程
根據(jù)能量守恒定律,粘性流體流動中的能量交換可用下列能量平衡方程加以描述:

-潤滑油的密度
-潤滑油的比熱系數(shù)
溫度起始條件: ,
由于油膜厚度與軸瓦徑向、周向尺寸相比很小,故在油膜的內(nèi)外側(cè)泄邊的邊界條件假設(shè)為絕熱,即:
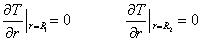
瓦塊的溫度分布由瓦塊的熱傳導(dǎo)方程求出。由熱力學(xué)可知,瓦塊的溫度控制方程為:
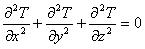
假設(shè):
(1) 物體是均勻且各向同性的;
(2) 導(dǎo)熱系數(shù) 、比熱容 及密度 均為常數(shù);
(3) 物體內(nèi)部沒有溫度躍變;
(4) 軸承系統(tǒng)為穩(wěn)定導(dǎo)熱, ;
(5) 系統(tǒng)無內(nèi)熱源;
轉(zhuǎn)化為圓柱坐標(biāo)形式如下:

-是瓦塊厚度方向的坐標(biāo)
軸瓦熱傳導(dǎo)方程的邊界條件:油膜與軸瓦界面保持熱流連續(xù)
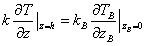
-瓦塊內(nèi)的溫度梯度 , 油膜內(nèi)溫度梯度
3、 溫粘方程
一般潤滑油的動力粘度隨溫度升高而很快降低。其關(guān)系可由近似的經(jīng)驗(yàn)公式表示,常采用如下的Reynolds粘溫關(guān)系式:

其中: 是潤滑油的溫粘指數(shù), 為在溫度 下潤滑油粘度(Pa*S)。
以上是推力軸承運(yùn)動方程式,據(jù)此方程組采用數(shù)值分析方法編程求解推力軸承的壓力分布、油膜厚度分布、溫度分布、軸承的功耗、軸承所需的潤滑油流量等參數(shù)。
(二)原推力軸承的計算參數(shù)及承載能力的計算
該軸承為米切爾軸承結(jié)構(gòu),每組11塊瓦,線支撐對稱結(jié)構(gòu),軸承外徑為172mm,內(nèi)徑為110mm,瓦塊張角α約為24°,支點(diǎn)角β為11.50;各個瓦塊不能聯(lián)動,沒有均載結(jié)構(gòu),工作轉(zhuǎn)速4480r/min,潤滑油相當(dāng)于46#汽輪機(jī)油,進(jìn)油溫度45º;假設(shè)11塊瓦為均勻分配載荷,如下圖所示:
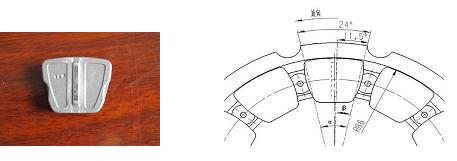
在上述條件下,用線支撐可傾瓦計算程序分別計算該推力軸承在不同的載荷下,推力軸承的最高點(diǎn)溫度、最小油膜厚度、最大油膜厚度等,如下表所示:
支點(diǎn)角β為11.50
主推力軸承載荷,N |
最高瓦溫,℃ |
最小\最大油膜厚度mm |
平均油膜壓力MPa |
最大油膜壓力MPa |
6600 |
77.3 |
0.0249\0.0296 |
0.655 |
1.36 |
8800 |
81.0 |
0.0224\0.0276 |
0.874 |
1.81 |
11000 |
84.3 |
0.0205\0.0259 |
1.09 |
2.26 |
13200 |
87.4 |
0.0189\0.0246 |
1.31 |
2.71 |
15400 |
90.3 |
0.0175\0.0234 |
1.53 |
3.15 |
17600 |
93.0 |
0.0166\0.0225 |
1.75 |
3.59 |
19800 |
95.6 |
0.0156\0.0216 |
1.97 |
4.03 |
22000 |
98.2 |
0.0148\0.0208 |
2.18 |
4.47 |
24200 |
101.0 |
0.0140\0.0201 |
2.40 |
4.91 |
26400 |
103. |
0.0134\0.0195 |
2.62 |
5.35 |
28600 |
105 |
0.0128\0.0189 |
2.84 |
5.78 |
30800 |
108 |
0.0122\0.0184 |
3.06 |
6.22 |
如果將支點(diǎn)角β改為12.50,其余條件不變的情況下,再分別計算該推力軸承在不同的載荷下,推力軸承的最高點(diǎn)溫度、最小油膜厚度、, 最大油膜厚度等,如下表所示:
支點(diǎn)角β為12.50
主推力軸承載荷,N |
最高瓦溫,℃ |
最小\最大油膜厚度mm |
平均油膜壓力MPa |
最大油膜壓力MPa |
6600 |
59.8 |
0.0393\0.0587 |
0.655 |
1.38 |
8800 |
62.9 |
0.0339\0.0526 |
0.874 |
1.83 |
11000 |
65.7 |
0.0301\0.0483 |
1.09 |
2.28 |
13200 |
68.3 |
0.0273\0.0450 |
1.31 |
2.73 |
15400 |
70.7 |
0.0250\0.0423 |
1.53 |
3.18 |
17600 |
73.0 |
0.0231\0.0401 |
1.75 |
3.63 |
19800 |
75.1 |
0.0216\0.0382 |
1.97 |
4.08 |
22000 |
77.2 |
0.0202\0.0366 |
2.18 |
4.53 |
24200 |
79.2 |
0.0191\0.0352 |
2.40 |
4.98 |
26400 |
81.2 |
0.0180\0.0339 |
2.62 |
5.42 |
28600 |
83.1 |
0.0171\0.0328 |
2.84 |
5.86 |
30800 |
84.9 |
0.0163\0.0318 |
3.06 |
6.63 |
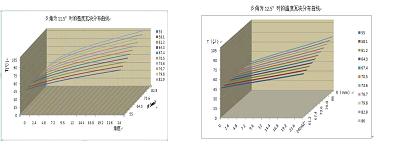
支點(diǎn)角β為11.50 °時溫度分布圖 支點(diǎn)角β為12.50 °時溫度分布圖

支點(diǎn)角β為11.50 °最小油膜厚度分布圖 支點(diǎn)角β為12.50 °時最小油膜厚度分布圖

在不同的載荷以及支點(diǎn)角β的情況下,軸承的最高溫度曲線
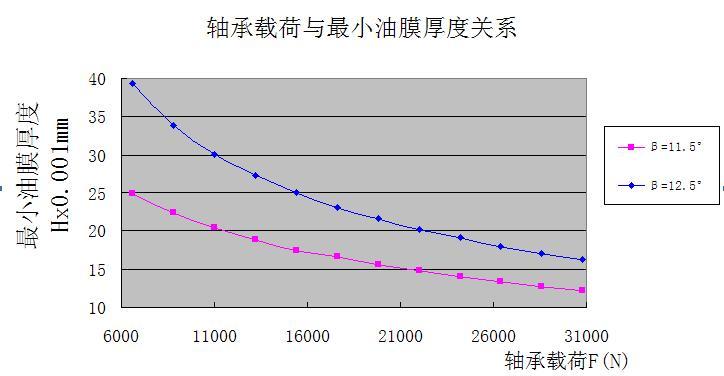
在不同的載荷以及支點(diǎn)角β情況下,軸承的最小油膜厚度曲線
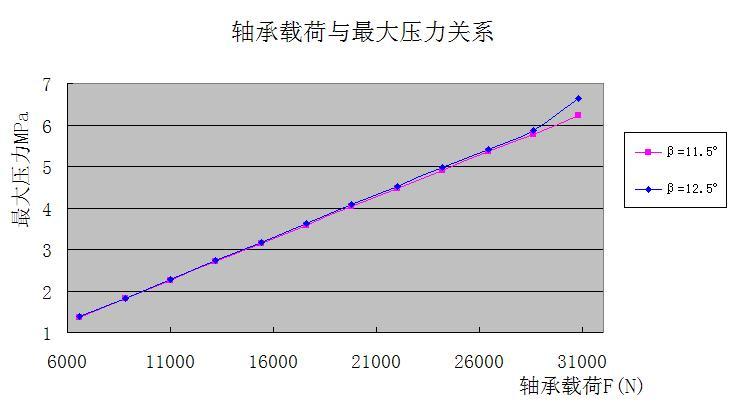
在不同的載荷以及支點(diǎn)角β情況下,軸承的最大壓力曲線
計算結(jié)果表明當(dāng)軸承所受推力為19800N時,瓦塊的最高溫度點(diǎn)達(dá)到95.6℃,最高溫度達(dá)到安全運(yùn)行的上限溫度。可以認(rèn)為大亞灣及嶺澳核電站的推力軸承在工作轉(zhuǎn)速為4480r/min,進(jìn)油溫度為45º的條件下,軸承安全承載能力小于2000公斤的載荷。
從圖中可以看出在相同的載荷下,支點(diǎn)角β為12.50 °比支點(diǎn)角β為11.50 °時,軸承的最高溫度大大下降,最小油膜厚度加厚,但軸承的最大壓力幾乎沒有上升,大大地提高軸承的安全運(yùn)行。或者說支點(diǎn)角β為12.50 °比支點(diǎn)角β為11.50 °有更高的承載能力。
從分析計算中可知,推力瓦塊在瓦塊幾何條件、工作轉(zhuǎn)速和進(jìn)油溫度不變的情況下,瓦塊的油膜溫度、瓦塊的油膜壓力和推力載荷的大小幾乎是成正比關(guān)系,油膜溫度分布是在進(jìn)油口最低出油口最高、油膜壓力最大位置是在瓦塊的中心部位,如下圖所示:
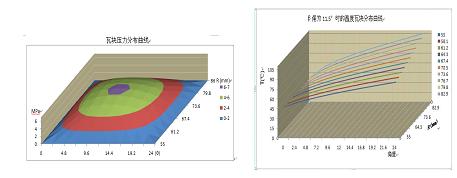
油膜壓力分布圖 油膜溫度分布圖
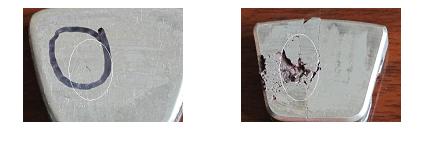
圖中框選為1-9號瓦塊 10號瓦塊嚴(yán)重龜裂區(qū)域
細(xì)微龜裂開始區(qū)域
從1-9號瓦塊和10號瓦塊可以看出框選位置是相同的位置也是龜裂最早發(fā)生的區(qū)域和后來龜裂最嚴(yán)重的區(qū)域,為什么呢?從油膜溫度分布圖和油膜壓力分布圖可知該區(qū)域溫度和壓力都相對較高,該區(qū)域的油膜溫度X該區(qū)域的壓力的積大于框選區(qū)域外的油膜溫度X區(qū)域外的壓力的積,是高溫高壓聯(lián)合作用使得該區(qū)域發(fā)生龜裂現(xiàn)象的。
實(shí)際上推力瓦塊在運(yùn)行中,在一定的時間內(nèi)合金面各點(diǎn)溫度的變化是很小的,但合金面各點(diǎn)油膜壓力隨著推力盤在轉(zhuǎn)動過程中發(fā)生軸向跳動而不斷地發(fā)生變化,變化的頻率就是轉(zhuǎn)速的大小。推力盤轉(zhuǎn)動跳動越大,各點(diǎn)的油膜壓力變化就越大,這種跳動是無法消除的,所以各點(diǎn)的油膜壓力變化也是一直存在的。在框選范圍內(nèi)由于合金受到的動壓載荷也最大,溫度相對較高,隨著循環(huán)次數(shù)的增加,合金面就逐漸產(chǎn)生動壓疲勞,合金在高溫下疲勞強(qiáng)度下降,更容易產(chǎn)生疲勞,合金開始逐漸產(chǎn)生疲勞裂紋,又隨著循環(huán)次數(shù)的增加,裂紋逐漸延伸并向深部發(fā)展,局部油膜破裂,又會產(chǎn)生更高的局部溫度,巴氏合金表面產(chǎn)生微熔化,如此反復(fù),裂紋范圍越來越大,最終形成象10號瓦塊框選范圍那樣的裂紋,此區(qū)域已經(jīng)完全不能承載,油膜出口區(qū)域也形成不了油膜隨之龜裂。
軸承合金發(fā)生龜裂的根本原因是由油膜動力學(xué)的機(jī)理來決定,只有合理結(jié)構(gòu)的軸承和設(shè)計合理的軸承參數(shù)才能夠避免合金面的損傷與龜裂。
(三)推力盤瓢偏對各個瓦塊受力的影響
推力軸承運(yùn)行時,推力盤瓢偏直接使各個瓦塊和推力盤間的距離不相等,形成各個瓦塊受力不均勻。
只單純考慮推力盤瓢偏,不考慮其它因素的影響,則無論什么情況下推力盤和瓦塊的幾何關(guān)系都會如下圖所示。
h:為瓦塊與推力盤的最小距離,也就是推力軸承和推力盤之間的最小油膜厚度之處
Δ:瓢偏量
為了保證安全運(yùn)行,認(rèn)為推力瓦塊與推力盤間的最小油膜厚度h不小于0.01mm
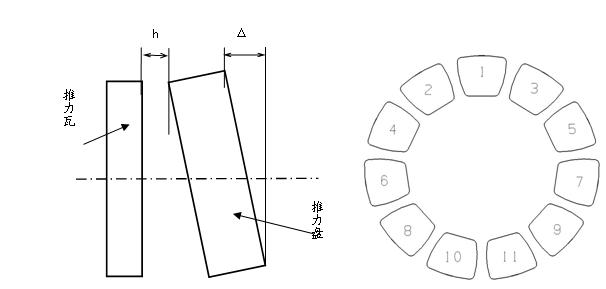
在某瞬間,設(shè)1號瓦塊與推力盤最小距離為0.01mm;則在不同的瓢偏量Δ下,各個瓦塊N與推力盤的最小距離h如下表所示:
h N
Δ |
10 |
8 |
6 |
4 |
2 |
1 |
3 |
5 |
7 |
9 |
11 |
0.03 |
0.04 |
0.0353 |
0.0275 |
0.0189 |
0.0124 |
0.01 |
0.0124 |
0.0189 |
0.0275 |
0.0353 |
0.04 |
0.06 |
0.07 |
0.0606 |
0.0449 |
0.0279 |
0.0149 |
0.01 |
0.0149 |
0.0279 |
0.0449 | <, TD vAlign=top width=47>
0.07 | |
0.09 |
0.10 |
0.0859 |
0.0625 |
0.0369 |
0.0173<, /DIV> |
0.01 |
0.01, , , 73 |
0.0369 |
0.0625 |
0.0859 |
0.10 |
0.12 |
0.13 |
0.1112 |
0.0799 |
,
0.0458 |
0.0197 |
0.01 |
0.0197 |
0.0458 |
0.0799 |
0.1112 |
0.13 |
由于圖形對稱,2、4、6、8、10瓦塊分別與3、5、7、9、11瓦塊到推力盤的距離相等。
根據(jù)上表中的各個瓦塊到推力盤的最小距離(亦即為最小油膜厚度),在實(shí)際工況參數(shù)和不同的瓢偏量下,從載荷--最小油膜厚度曲線圖中可大致查出各個瓦塊的實(shí)際承載載荷如下表:
,
F N
Δ |
10 |
8 |
6 |
4 |
2 |
1 |
3 |
5 |
7 |
9 |
11 |
0.03 |
100 |
200 |
400 |
1200 |
2800 |
4000 |
2800 |
1200 |
400 |
200 |
100 |
0.06 |
0 |
0 |
10 |
600 |
2000 |
4000 |
2000 |
600 |
10 |
0 |
0 |
0.09 |
0 |
0 |
0 |
200 |
1400 |
4000 |
1400 |
300 |
0 |
0 |
0 |
0.12 |
0 |
0 |
0 |
0 |
1100 |
4000 |
1100 |
0 |
0 |
0 |
0 |
從上表可知隨著瓢偏量的增大部分瓦塊已不再承擔(dān)載荷,各個瓦塊承受的載荷極不均勻,載荷明顯集中到部分瓦塊上。
在不同的瓢偏量下,推力軸承總的最大安全載荷如下:
瓢偏量(mm) |
0.03 |
0.06 |
0.09 |
0.12 |
推力軸承安全載荷(N) |
13400 |
9220 |
7400 |
6200 |
以上只從瓢偏量單一因素計算出來的結(jié)果,實(shí)際上由于各個部件會有些彈性變形等因素的影響,使得各個瓦塊的實(shí)際承載的載荷要均勻一些,情況并非如此惡劣。但如果瓢偏量過大,載荷一定是會相對集中的。
(四)GB/T 18844-2002中有關(guān)巴氏合金損傷形成原因的概述及照片
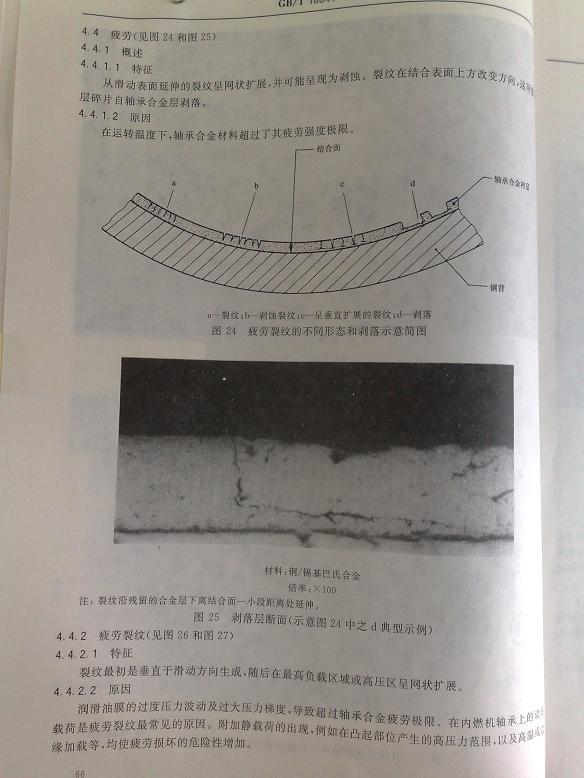
疲勞裂紋特征:裂紋最初是垂直于滑動方向生成,隨后在最高負(fù)載區(qū)或高壓區(qū)呈網(wǎng)狀擴(kuò)展,并可能呈現(xiàn)為剝蝕。裂紋在結(jié)合面上方改變方向,導(dǎo)致襯層碎片自軸承合金層剝離。
疲勞裂紋原因:潤滑油膜的過渡壓力波動及過大壓力梯度,導(dǎo)致超過軸承合金疲勞極限。在高壓力范圍以及高溫或邊緣加載等,均使疲勞損壞的危險性增加。
10號瓦塊裂紋與以上描述一致,可以斷定10號瓦塊為動壓疲勞裂紋。
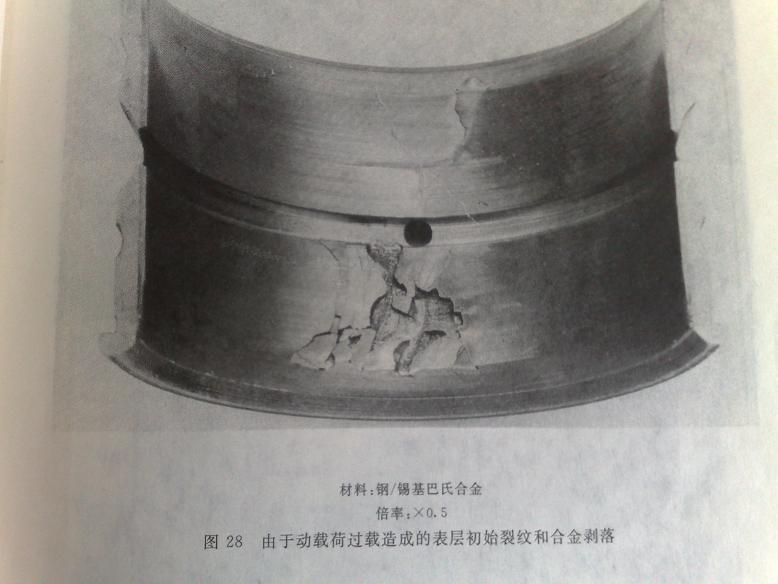
上圖由于動載荷過載造成的合金表層初始裂紋和合金剝落。
特征是在最高負(fù)載區(qū)有界限分明的大范圍軸承合金剝離,露出鋼層表面。
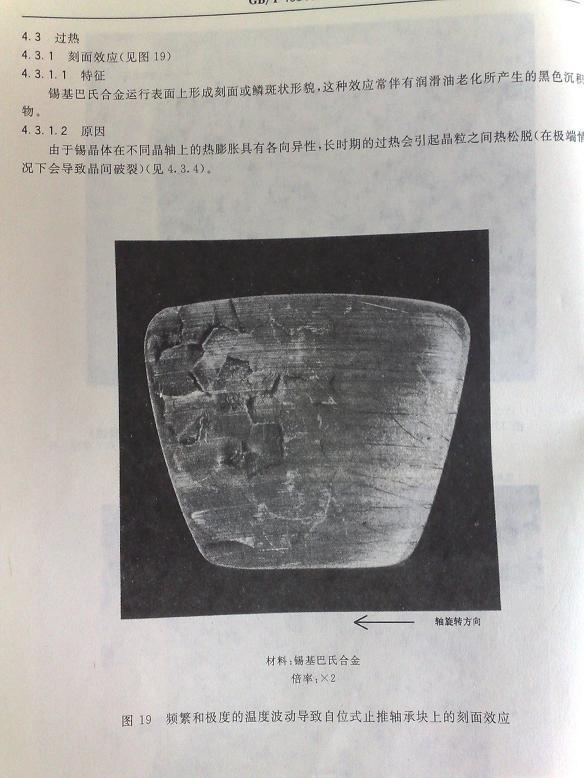
右圖刻面效應(yīng):巴氏合金運(yùn)行表面上形成刻面或魚鱗狀形貌是由頻繁和極度的溫度波動導(dǎo)致的。
原因:由于錫晶體在不同晶軸上的熱膨脹具有各向異性,長期的過熱會引起晶粒之間熱松動。
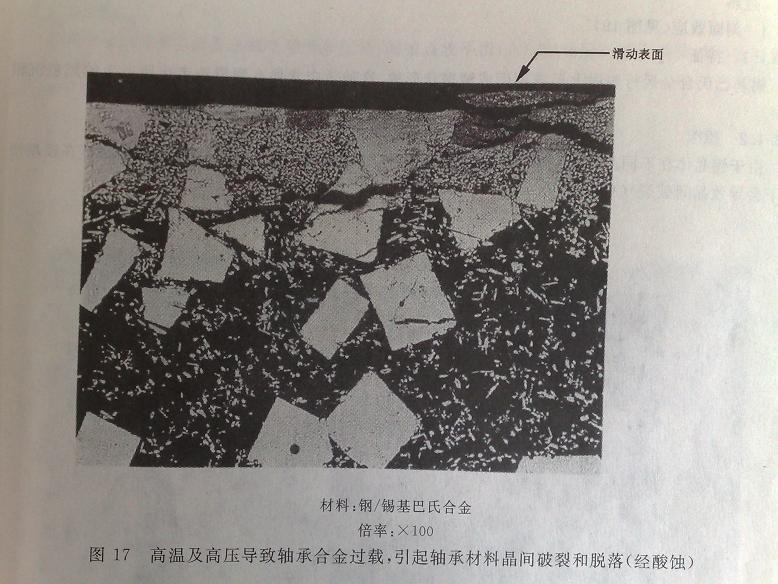
左圖為高溫及高壓導(dǎo)致軸承合金過載,引起軸承材料晶間破裂和脫落。
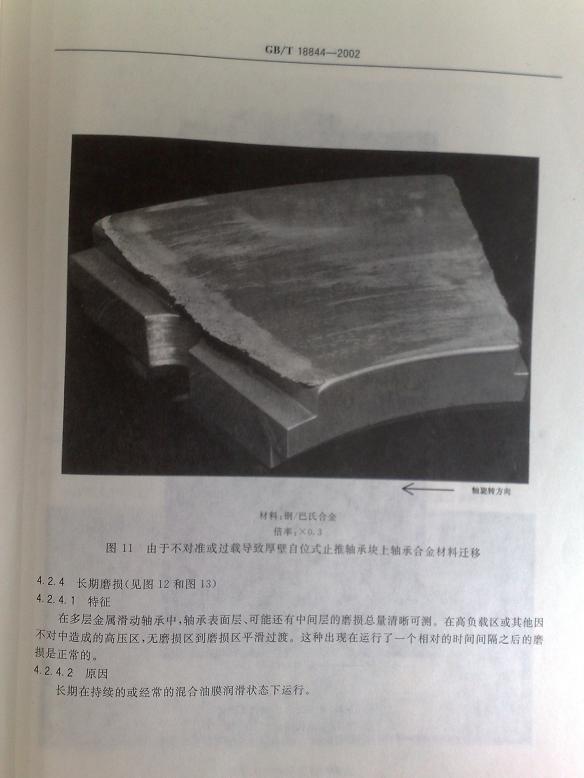
1、強(qiáng)行啟動、軸承表面材料涂抹或遷移
特征:軸承表面平滑,遷移材料沿旋轉(zhuǎn)方向延伸為舌狀凸起。
扇形推力瓦塊在表面摩擦高溫下遭到顯著磨損,常常表現(xiàn)為軸承合金材料磨損后從瓦塊一端沿著旋轉(zhuǎn)方向沉積到另一端邊緣上。
原因:在極端運(yùn)轉(zhuǎn)條件(負(fù)載啟動或低速運(yùn)行)下,配合表面短暫而劇烈地接觸、過熱、間隙不當(dāng)或幾何形狀缺陷而出現(xiàn)初始混合油膜潤滑。
2、初始熔融和熔化導(dǎo)致的材料遷移
特征:初始熔融或軸承材料中低熔點(diǎn)組元熔化,通常是咬粘及粘著特征相聯(lián)系的結(jié)果。重新凝固的合金呈現(xiàn)珠狀或條紋狀。軸承表面通常已經(jīng)變色。原因是在明顯的混合油膜潤滑期間,熱量迅速增加并導(dǎo)致大范圍過熱。
大亞灣D2RCV001PO的9塊主推力瓦塊,自編號為1號—9號。表面合金層有與以上相同的損傷現(xiàn)象。
十、 推力軸承啟動及承載能力實(shí)驗(yàn)
1、上充泵推力軸承試驗(yàn)機(jī)的結(jié)構(gòu)簡圖
1 |
2 |
3 |
4 |
5 |
6 |
7 |
8 |
9 |
試驗(yàn)臺架如上圖,主要由潤潤滑油泵(1)、潤滑油油箱(2)、潤滑油冷卻水箱(3)、試驗(yàn)機(jī)(4)、潤滑油過濾器(5)、載荷加載機(jī)構(gòu)驅(qū)動電機(jī)(6)、溫度顯示儀(7)、電機(jī)(8)、試驗(yàn)機(jī)支持架(9)、等設(shè)備組成。下圖為試驗(yàn)機(jī)結(jié)構(gòu)圖。
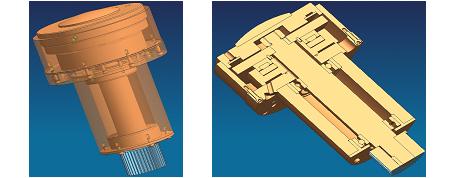
2、 試驗(yàn)機(jī)設(shè)計、制造、試驗(yàn)安排
4月1日-4月30日試驗(yàn)機(jī)結(jié)構(gòu)設(shè)計
5月1日-6月30日試驗(yàn)機(jī)各零件制造
7月1日-7月30日試驗(yàn)機(jī)安裝調(diào)試
8月1日-10月30日進(jìn)行試驗(yàn)
3、上充泵軸瓦啟動磨損試驗(yàn)
模擬對象及工況:
大亞灣核電站上充泵驅(qū)動端軸承室設(shè)計有專門的油池,供上充泵應(yīng)急啟動時潤滑使用。上充泵應(yīng)急啟動中,以推力盤做粘度油泵,通過推力盤的旋轉(zhuǎn)帶動油循環(huán),實(shí)現(xiàn)對推力軸承的強(qiáng)制潤滑。上充泵每月一次需要進(jìn)行應(yīng)急啟動工況下的驗(yàn)證試驗(yàn),在輔助潤滑油泵開啟0或5秒后上充泵開始啟動并立刻轉(zhuǎn)入高速帶載,在輔助潤滑油泵啟動之前油池之下的推力軸瓦和部分推力盤浸在潤滑油中,油池之上的推力瓦塊表面只是殘留少些潤滑油。
為避免試驗(yàn)機(jī)設(shè)計過于復(fù)雜,本試驗(yàn)機(jī)中未設(shè)計專門油池。本次試驗(yàn)?zāi)M對象是主要位于油池之上的推力瓦塊,本次試驗(yàn)?zāi)M工況為其在缺油狀態(tài)下的帶載啟動工況,此工況下瓦塊尚未建立有效的油膜。本次試驗(yàn)轉(zhuǎn)速為4480r/min,四個主推力瓦塊對稱分布。具體結(jié)構(gòu)見下圖。試驗(yàn)中,試驗(yàn)機(jī)上逐步加載負(fù)荷,每次加載后試驗(yàn)機(jī)在缺油情況下點(diǎn)動啟動100次,解體試驗(yàn)機(jī),對推力軸承磨損情況進(jìn)行檢查拍照,直至軸瓦被破壞結(jié)束本次試驗(yàn)
第一次試驗(yàn):總載荷為16KG,一個瓦塊承受載荷為4KG,啟動100次,檢查瓦塊表面沒有明顯變化,見下圖:
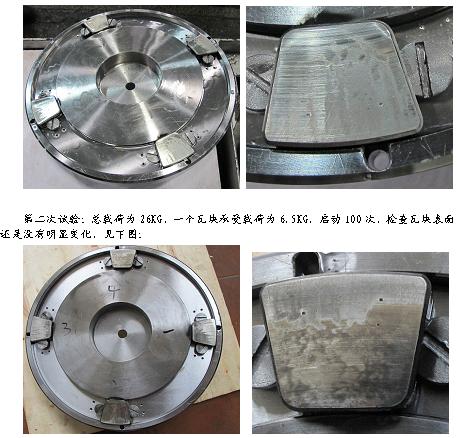
第三次試驗(yàn):總載荷為36KG,一個瓦塊承受載荷為9KG,啟動100次,檢查瓦塊合金表面有明顯的遷移變化,合金表面發(fā)黑。見下圖:
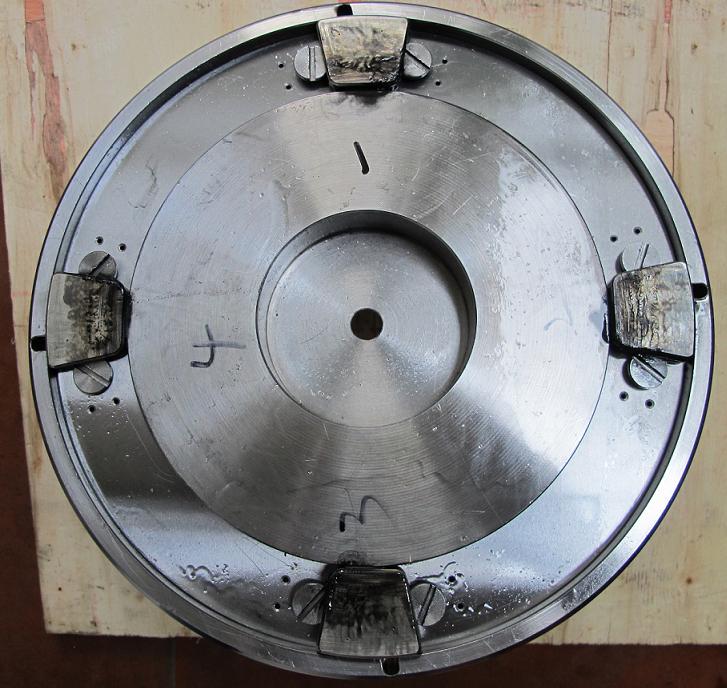
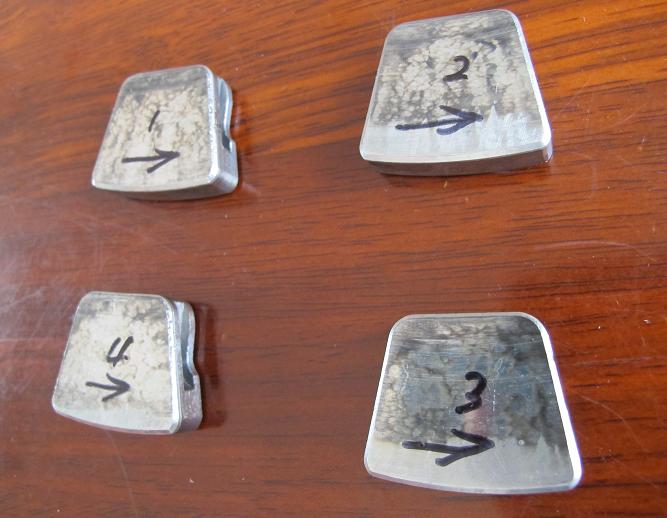
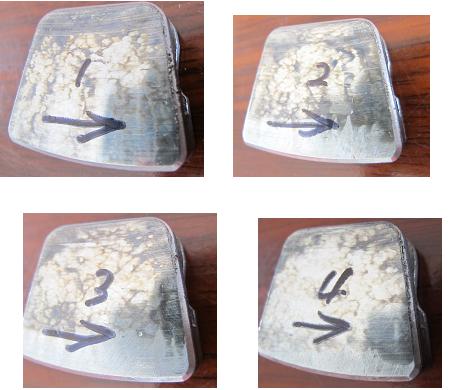
本次試驗(yàn)結(jié)果表明,推力瓦塊在尚未建立充分的油膜情況下,在經(jīng)歷100次帶載啟動后發(fā)生了合金材料遷移現(xiàn)象。瓦塊與推力盤間的潤滑油膜在高溫高熱的影響下發(fā)生了碳化現(xiàn)象。
4、 軸承承載能力實(shí)驗(yàn)
本次試驗(yàn)是上充泵主推力軸承在工況條件下,隨著載荷的增加,觀察推力瓦塊的溫度變化。
實(shí)驗(yàn)軸承轉(zhuǎn)速為4480r/min;取上充泵主推力四個瓦塊(編號為14、15、16、17),對稱分布在軸承座上,每個瓦塊都埋入溫度傳感器,型號為Pt100。
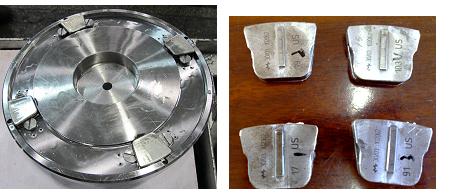
軸承在各載荷及進(jìn)油溫度下,測得各個瓦塊溫度如下表:
軸承載荷(N) |
進(jìn)油溫度℃ |
14#瓦溫℃ |
15#瓦溫℃ |
16#瓦溫℃ |
17#瓦溫℃ |
3850 |
45 |
58 |
56 |
54 |
58 |
5680 |
45 |
63 |
61 |
59 |
63 |
7520 |
45 |
69 |
67 |
65 |
70 |
9350 |
45 |
73 |
70 |
71 |
75 |
11180 |
45 |
78 |
75 |
73 |
79 |
|
|
|
|
|
|
|
|
|
|
|
|
實(shí)驗(yàn)結(jié)果顯示在一定的載荷下,瓦塊的實(shí)際測量溫度比理論計算溫度要小5℃左右,誤差主要原因:一是計算瓦溫時將瓦塊認(rèn)為是剛性的,實(shí)際上瓦塊在載荷下是要產(chǎn)生彈性變形;二是在計算時瓦塊的幾何條件與實(shí)際的幾何形狀不是完全吻合的。所以形成計算結(jié)果與實(shí)驗(yàn)結(jié)果有一定的誤差,但誤差也不是太大。
實(shí)驗(yàn)結(jié)果表明在一定的條件下瓦塊的溫度隨著載荷的加大而加大,溫度趨勢也是和計算結(jié)果一致。
十一、分析討論
根據(jù)故障軸承的現(xiàn)場檢測情況及軸承的結(jié)構(gòu),經(jīng)過計算分析,軸承故障的原因可以總結(jié)出以下幾點(diǎn):
1、從計算結(jié)果來看,當(dāng)該軸承載荷(機(jī)組軸向力)為30800KG時,推力瓦塊最高點(diǎn)溫度達(dá)到108℃,溫度已達(dá)到軸承報警溫度(國內(nèi)進(jìn)口機(jī)組軸承報警溫度有的最高設(shè)置到110℃,國內(nèi)機(jī)組大部分設(shè)置為85℃-90℃)
2、軸承的安裝誤差、制造誤差以及轉(zhuǎn)子的繞動是不可避免的,當(dāng)機(jī)組運(yùn)行時,不可能使11個瓦塊與推力盤等距和平行,必然使11個瓦塊不能夠均勻承載,會使得載荷集中到部分推力瓦塊上,溫度升高,導(dǎo)致過載超溫,引起瓦塊損傷失效。L1RCV003PO推力盤瓢偏為 0.12mm,在只單純考慮瓢偏的情況下,計算分析表明載荷嚴(yán)重集中,大部分瓦塊不承載。
3、大亞灣D2RCV001PO的9塊主推力瓦塊,自編號為1號—9號。每個瓦塊都不斷地受到動載荷沖擊或負(fù)載啟動,將合金面形成混合潤滑并產(chǎn)生遷移,每塊瓦塊在相同的區(qū)域已經(jīng)產(chǎn)生細(xì)微的疲勞裂紋。
4、大亞灣及嶺澳核電站推力瓦塊的合金成分基本符合標(biāo)準(zhǔn)牌號合金ZSn8Cu4成分;嶺澳1#機(jī)L1RCV003PO合金銅含量偏低。合金金相顯示巴氏合金金相組織不均勻、嚴(yán)重偏析;在相同的工況條件下,組織的良好與否會相對影響到合金的耐磨性和使用壽命。
5、 軸承合金發(fā)生龜裂的根本原因是由油膜動力學(xué)的機(jī)理來決定的,只有合理結(jié)構(gòu)的軸承和設(shè)計合理的軸承參數(shù)才能夠避免合金面的損傷與龜裂。
上海大學(xué)軸承研究所
朱禮進(jìn)